Trygons SA is one of Change2Twin beneficiaries who are now in the middle of deploying their first digital twin. When we first met in person, it was September 2023, the kickoff meeting for all experiments. Since then, they have gone a long way creating, testing, validating their digital twin. Now they are in the final phase of their Change2Twin-funded experiment and are convinced to work on it further. Their mentor (and our project colleague), Anna Sumereder from BOC Group, is happy about their progress. So let us introduce you Trygons SA and their digital twin project!
Who is Trygons SA?
Trygons SA, located in Keratea Attikis, Greece, is a trailblazing manufacturer with a focus on composite parts for the marine and automotive industries. Employing 24 experts, the company excels in crafting medium to large-sized, intricately reinforced structures, particularly targeting high production volumes. Trygons is renowned for its in-house Research & Development capabilities and the utilization of cutting-edge technologies that facilitate the design and fabrication of these advanced components.
Expertise in single-shot infusion techniques
The firm is distinguished not only for its robust production capabilities but also for its innovative approach to manufacturing. Trygons specializes in single-shot infusion techniques, enhancing the quality and cost-effectiveness of parts. This method allows them to produce glass or carbon-fiber structures in significantly less time and at a lower cost compared to traditional methods. Their expertise in lightweight and fuel-efficient designs has led to groundbreaking achievements, such as setting a world record with Herbert Nitsch’s free-diving exploits and achieving notable reductions in vessel weight and fuel consumption with projects like the Aegean EcoRun Project.
Overall, Trygons is not just a parts manufacturer; it is a hub of innovation where complex concepts are transformed into tangible, market-leading products that push the boundaries of what is possible in composite manufacturing.
What is the purpose of their digital twin?
The purpose of the digital twin created and deployed for the Gelcoating process is to achieve a comprehensive, high-fidelity replication and monitoring of this complex manufacturing operation. By integrating sensors and digital technologies, the digital twin accurately tracks and analyzes the details of the gelcoating process, which is crucial for ensuring the quality of the final product. This includes the precise spraying of the correct quantity of gelcoat onto the mold, which heavily influences the product’s external appearance and initial quality assessments by customers. The digital twin employs sophisticated sensory technology to track parameters such as speed, acceleration, flow control, and total material sprayed. Additionally, by evaluating the quantity of material used per application, the digital twin can indirectly monitor the remaining quantities in the tanks, facilitating precise material management without the need for direct measurement. This comprehensive monitoring ensures that each phase of the gelcoating process meets stringent quality standards.
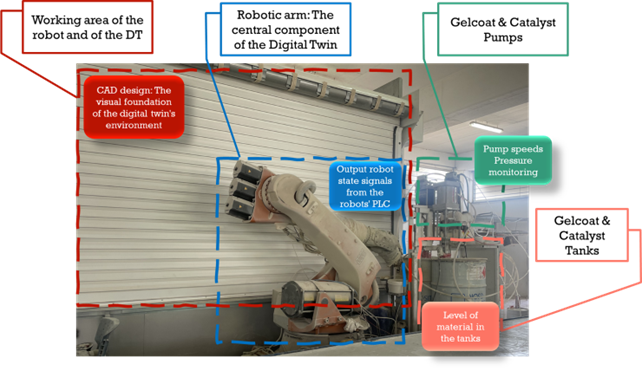
Twinning of pumps
In the context of the Change2Twin project, our primary focus is on implementing the twinning of the pumps, which constitutes the most critical and, concurrently, the most intricate aspect of the entire system. To achieve this, we will employ two rotary encoders to continuously monitor the speed, acceleration, and position of these two pumps as well as a pressure sensor for monitoring the working pressure of the pumps. Through a post-processing analysis of the data collected from these rotary encoders, combined with our knowledge of the volumetric specifications of the pumps, we will have the capability to not only detect the total sprayed material accurately but also identify various issues that signal the need for maintenance. One notable example is the potential reduction in pump speed and, subsequently, a decrease in the total sprayed material when the pump filters become obstructed.
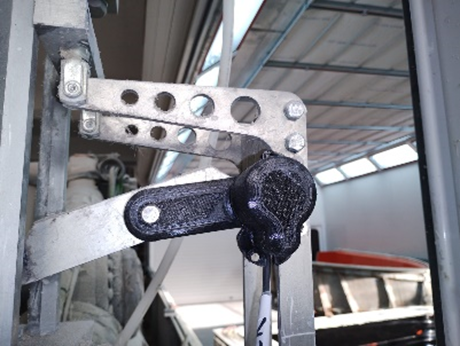
Functional purposes of digital twin
Moreover, the implementation of the digital twin serves several functional purposes:
- Optimization of Process Parameters: By continuously monitoring and analyzing the data from various sensors, the digital twin helps in fine-tuning the interconnected parameters that influence the gelcoating process. This ensures that the materials are sprayed in the correct quantities and with minimal fluctuation in layer thickness, crucial for achieving the desired product quality.
- Predictive Maintenance: The digital twin enables predictive maintenance by identifying potential issues such as pump blockages or filter obstructions before they lead to downtime or defective products. This proactive approach reduces maintenance costs and increases operational efficiency.
- Quality Assurance: The precise control and monitoring capabilities of the digital twin ensure that the gelcoat is applied consistently and correctly, which is vital for the product’s aesthetic and functional quality.
- Remote Monitoring: Remote monitoring capabilities enable operational oversight from distant locations, facilitating real-time adjustments and decisions to maintain continuous production and prevent quality issues. This feature adds a critical layer of flexibility and responsiveness to the manufacturing process.
- Scalability and Extension: Initially and for the scope of the project we focused on twinning the pumps, however after the completion of the project we aim to continue improving the digital twin to extend these capabilities to include all subsystems of the gelcoating process, thereby creating a fully integrated and comprehensive digital twin. This scalable approach allows for broader application and continuous improvement across the entire manufacturing operation.
In summary, the digital twin is designed to enhance the gelcoating process through detailed monitoring and optimization, ensuring product quality, enabling predictive maintenance, and providing a scalable solution that can be extended to other parts of the manufacturing process.
Which improvements brought the digital twin to your company?
Even though the implementation of the digital twin for the Gelcoating process is still in its early stages and not fully completed, we are already beginning to leverage its remote monitoring capabilities. This feature allows for operational oversight from distant locations, enabling real-time adjustments and critical decision-making to maintain continuous production and minimize quality deviations. The remote monitoring aspect is particularly beneficial as it facilitates immediate responses to alerts for critical issues, such as complete blockages of the pumps or the spraygun, ensuring these problems can be addressed quickly to prevent downtime.
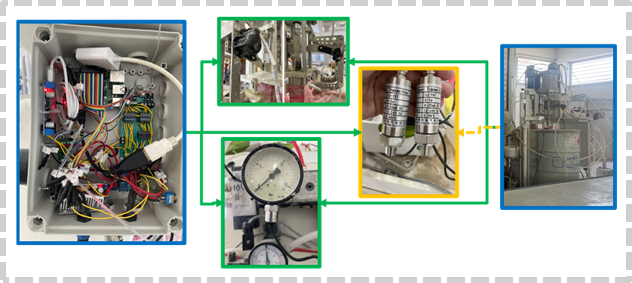
Adding AI components
Looking ahead, the advantages of the digital twin are expected to be significantly enhanced with the integration of an artificial intelligence (AI) component. This addition is anticipated to revolutionize the predictive maintenance capabilities of the digital twin. By analyzing data collected through continuous monitoring, the AI will help us identify potential issues before they escalate into critical problems. This proactive approach aims to resolve potential failures preemptively, ensuring that operations proceed without interruption and that we seldom, if ever, encounter critical moments. The incorporation of AI into the digital twin represents a forward-thinking step towards fully maximizing the technology’s potential to streamline production, enhance efficiency, and maintain the highest standards of quality.
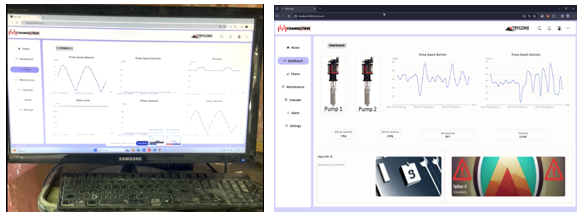
What are your plans for the near future with the digital twin?
Our plans for the near future is to further extend and optimise the capabilities of the digital twin for the Gelcoating process in order to fully capitalize on its potential:
- Feature Addition: We are set to enhance our existing digital twin model with several strategic updates
- Water Level Sensors: We plan to install water level sensors in the two tanks to monitor their levels with increased precision, providing a more detailed and accurate understanding of material usage.
- Raspberry Pi Housing Upgrade: The housing for the Raspberry Pi will be upgraded to meet industrial standards, ensuring its reliable operation and extending its longevity.
- Industrial Screen Integration: We intend to install a small industrial screen directly on the casing to display the dashboard on the production line, making it easily accessible and visible to operators.
- Dashboard Enhancements: We will refine the HMI of our dashboard and update it to include all the new features, thereby improving user interaction and functionality.
- Extension to Other Subsystems: Initially, our project concentrated on the twinning of the pumps, which are critical to the gelcoating process. Moving forward, we aim to extend the digital twin to encompass all subsystems involved in the process, such as the KUKA KRC2 robot equipped with the Graco spraygun, the pressurized catalyst supply system, and the industrial oven with its digitally regulated ventilation system. This expansion will create a fully integrated and comprehensive digital twin, covering every aspect of the manufacturing operation.
- Continuous Improvement and Optimization: We plan to continually refine and improve the digital twin by establishing introducing the ability of the AI model to constantly train on the new datasets collected and feedback. This ongoing optimization will help us fine-tune the process parameters further and also deal with parameters that are not currently considered such as change in material viscosity due to environmental temperature differences among seasons., ensuring even greater accuracy in material application and overall process efficiency.
References and project team
Project team in Trygons: Evagoras Zervas, Kozell Williams, Alexander Sarasitis
Website: https://trygons.com/
Project mentor from Change2Twin: Anna Sumereder, BOC Group
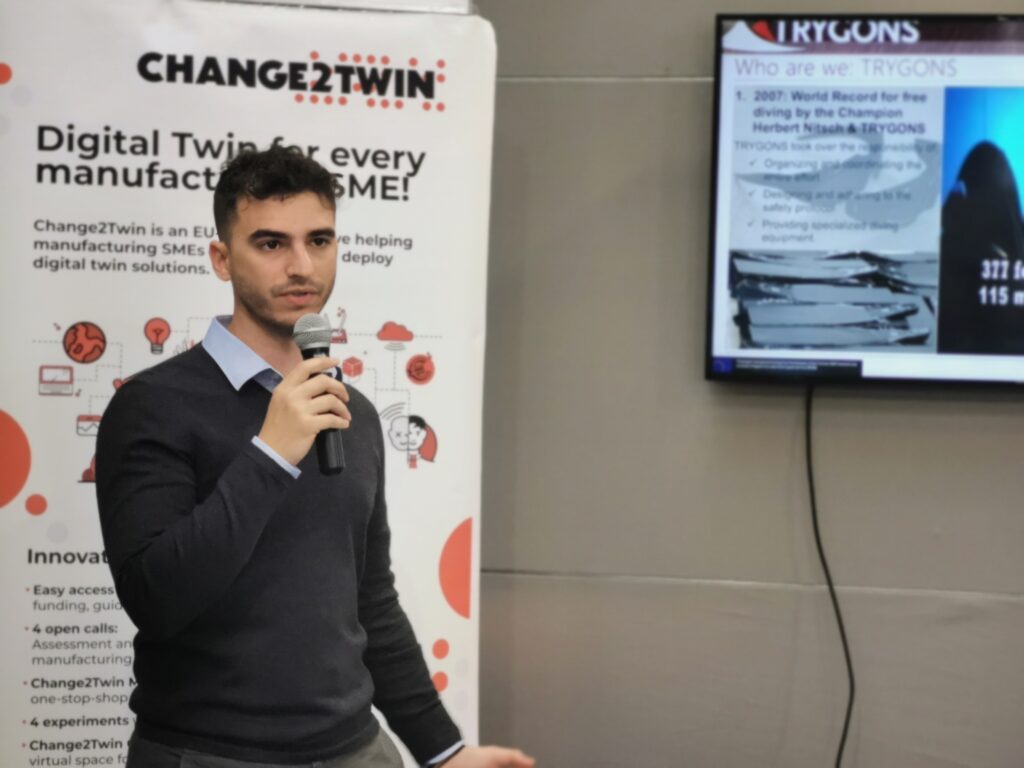
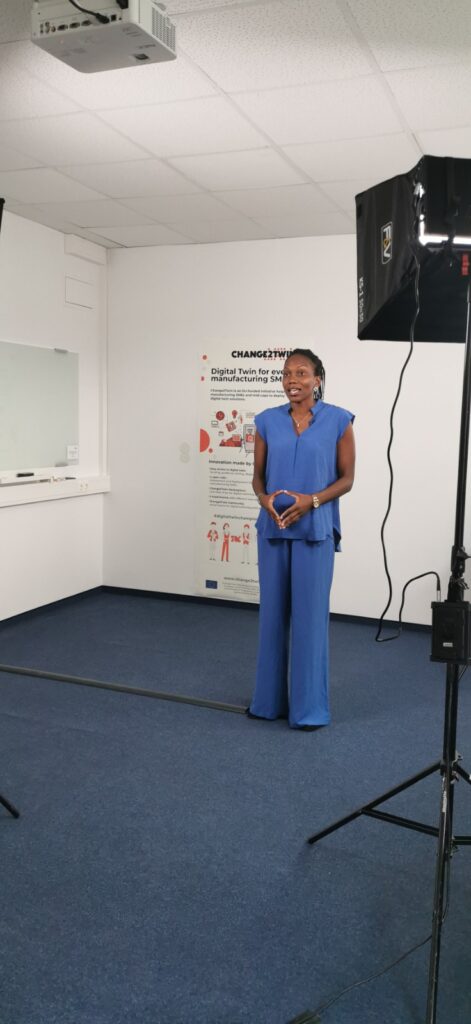
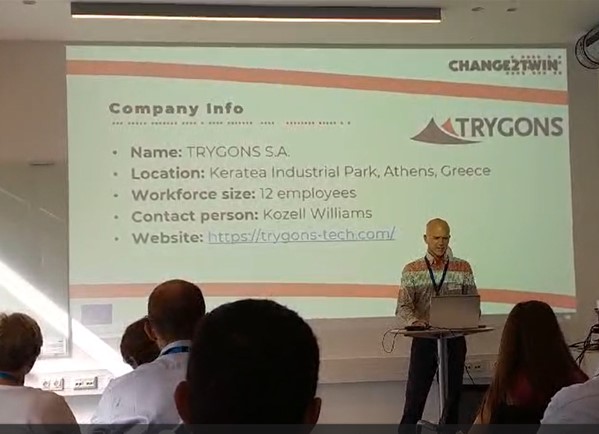